Microfued Sensor Technology
The VTM530 series Micro-fused pressure transmitters use strain gauges bonded on 17-4PH stainless steel diaphragm based on micro-fused glass frit technology. The strain gages with uniform resistance are obtained by growing an epi-silicon layer on a single crystal silicon wafer using the epitaxial deposition technique rather than conventional photolithography and etching techniques.
The inorganic micro-fused glass frits are used as the bonding material between the strain gauges and the 17-4PH diaphragm. Compared to organic adhesives, the glass frits bonding material can minimize the hysteresis error in high-temperature, high pressure applications and improve the mechanical properties of semiconductor strain gauge-based pressure transducers.
Specifications
-
High-accuracy
-
Compact and strong
-
Various high-pressure sealing and pressure ports are optional
-
CE and waterproof verification
-
High reliability
Description
-
Heavy industry application
-
One-body molding pressure cavity, no leakage, high reliability
-
Reverse protection
-
Output short circuit protection
-
Non-linear accuracy up to ± of 0.1%
-
Comprehensive accuracy up to ± 1.0%
-
Compact and strong
-
-50°C to + 120°C operating temperature
Overview
VORTORQ Sputtering thin film technology is an effective method for designing pressure sensors for demanding industries that require high temperatures and high-pressure capabilities. The key design considerations for a sputtered thin film pressure sensor include a wide pressure range, typically spanning from a few psi to several thousand psi, to accommodate the diverse operating conditions in such industries.
The sensor must also exhibit high sensitivity to detect even slight changes in pressure, coupled with a rapid response time to ensure real-time data collection. Temperature stability is crucial, as these industries often experience significant temperature fluctuations. Durability is another critical factor, as the sensor must withstand harsh conditions such as vibration, shock, and exposure to high temperatures and pressures.
By utilizing sputtering technology, thin films of materials like piezoresistive or piezoelectric substances can be deposited onto substrates, providing precise pressure sensing. Specialized packaging ensures the sensor remains robust against external stresses, while integrated circuitry amplifies the sensor's output for accurate data transmission.
As a result, sputtering-based thin film pressure sensors offer a reliable, high-performance solution for pressure measurement in demanding industrial applications.

Overview
VTMP710 flush diaphragm pressure sensor series adopts a state-of-the-art technical solution with a very sturdy flush steel measuring diaphragm. This technology makes the product unique and suitable for pressure measurement in dense, aggressive fluids and pastes.
A flush diaphragm is a type of diaphragm that is entirely open and exposed to the pressure media and level or slightly recessed to the surrounding surfaces when installed.
VTMP710 series offers an extensive range of transducers for pressure measurement in all industrial applications. In addition, models are available for special and high-precision applications and also for use in particularly heavy-duty and demanding environments, such as mobile vehicles.
In addition, this series introduces new membranes in miniaturized sizes which are the smallest of their kind on the market.
Overview
The VTMH530 hydrogen pressure sensor provides vital functions and is certified for measuring hydrogen pressure. This pressure sensor has been tested and approved for use in automotive applications based on the EC79 standard. The sensor has a 316L stainless steel sensing element that can fully control the hydrogen pressure. This primary sensor uses a cavity without welds or liquid filling to ensure long-term stability and operational functions. VTMH530 can be packaged for various storage tank pressure and fuel cell regulator applications.
The VTMH530 features VORTORQ's proprietary micro-fused technology or sputtering thin film pressure sensing element. The thread, hex, and diaphragm are machined from one piece of 316L SS, eliminating the risks associated with other sensor technologies, including media compatibility, weld failures, and contamination through an oil-filled cavity. The VTMH530 pressure sensors passed all tests, including media compatibility, aging, corrosion resistance, endurance testing, pressure cycling, leakage testing, isolation, noise compatibility, and hydraulic strength. The thick diaphragm of the 900 bar (13,053.4 PSI) pressure sensors held the 1,800 bar burst pressure test and continued to operate above 2,400 bar until the O-ring was extruded.
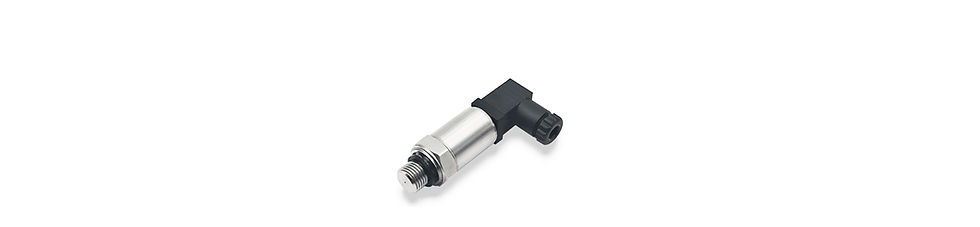
Specifications
-
Heavy Industrial CE Approval
-
10 V/m EMI Protection
-
Reverse Polarity Protection on Input
-
Short Circuit Protection on Output
-
Up to ±0.1%Accuracy
-
Up to ±0.5%Total Error Band
-
Compact Outline
-
-40℃…+125℃ Operating Temperature-20℃…+85℃ Compensated Temperature
Application
-
Military/Aerospace Test Stands
-
Automotive Test Stands
-
Calibration Equipment
-
High Accuracy Applications
-
Stationary Motor Fuel Control
-
High End Industrial Machinery
Application
• Environmentally friendly chemical coatings, polyurethane equipment
• Pressure control of food and medicine equipment
• Paint detection system
• Mud, mud pump, coal slurry, pulp, crude oil, asphalt, etc
• Oilfield drilling, logging, logging, offshore oil production platform
• Well measuring instruments, etc
• Other industrial sites requiring anti-blocking, high-strength vibration, and impact
Description
• Hard shell flat die, impact resistant
• Pressure range up to 10000psi
• Multiple pressure interfaces are optional
• Compensation temperature 0 ℃ - 70 ℃
• Nonlinear accuracy can reach ± 0.5%
• The comprehensive accuracy can reach ± 1.0%
• 0 ° C to+70 ° C compensation temperature
• - 50 ° C to+120 ° C operating temperature